Understanding Scheduling Complexity in Additive Manufacturing
In manufacturing, scheduling complexity grows exponentially with each additional work order and operation. To illustrate this, consider a simple scenario with three work orders each requiring four sequential operations:
- 10 PRINT
- 20 WIRE
- 30 TUMBLE
- 40 CLEAN
Exploring Permutations:
- First Operation (PRINT):
With three work orders, there are six permutations for the sequence in which the work orders flow through the first resource, PRINT. - Second Operation (WIRE):
Adding the second operation increases the permutations to 18. This represents all possible sequences for the work orders as they pass through both PRINT and WIRE. - Third Operation (TUMBLE):
Introducing the third operation expands the complexity further to 54 permutations, accounting for the sequence of all work orders through PRINT, WIRE, and TUMBLE. - Fourth Operation (CLEAN):
Including the fourth operation raises the total permutations to 162, representing all potential sequences through the entire production workflow. - Adding an Additional Work Order:
By introducing just one more work order, the permutations skyrocket to 768, illustrating how dramatically the scheduling complexity increases with even minor adjustments to work order volume.
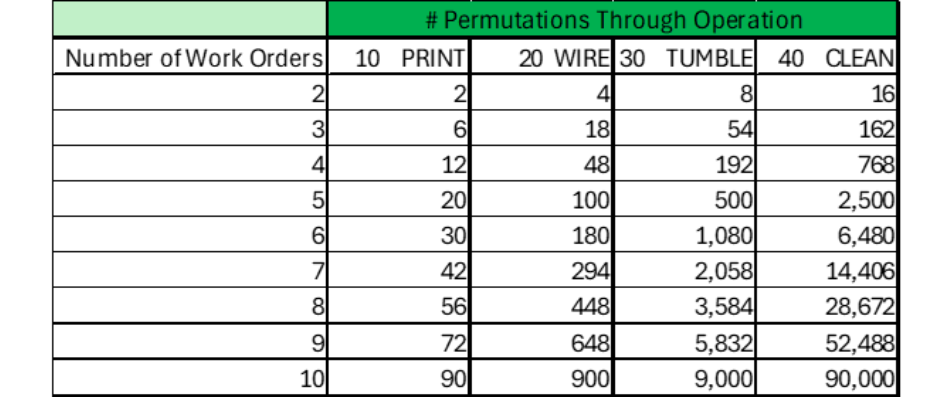
Formula for Scheduling Permutations:
The relationship governing these permutations can be expressed mathematically as:
P = WS(W-1)
Where:
- P= Number of Permutations
- W = Number of Work Orders
- s= Number of Operations
Considerations Beyond Basic Permutations:
The above example provides a simplified view of scheduling complexity. In real-world scenarios, the situation is far more intricate due to additional constraints present in additive manufacturing such as:
- Machine Count: The number of machines at each work center.
- Work Center Calendars and Shifts: The operational schedules of resources.
- Resource Qualification: Ensuring the right machines and personnel are to specific operations.
- Printer-Specific Material Availability: Predicting the material level at each printer at any given time, accounting for consumption from scheduled work.
These factors further compound the complexity, necessitating advanced scheduling software that can dynamically evaluate and optimize production plans in real time. Effective scheduling solutions, like nPower Scheduler™, leverage sophisticated algorithms to manage these challenges, enabling manufacturers to meet deadlines, reduce costs, and enhance efficiency.
Understanding and addressing scheduling complexity is not just a matter of calculation; it’s a cornerstone of operational success in modern additive manufacturing.
I will be publishing additional notes on scheduling complexity in the coming weeks to further illustrate how these work center and material constraints complicate the algorithms of optimal production scheduling.
David Bennett
Chief Product Officer, nPower Technologies